Ikhtisar Konektor Tegangan Tinggi
Konektor tegangan tinggi, juga dikenal sebagai konektor tegangan tinggi, adalah jenis konektor otomotif. Konektor ini umumnya mengacu pada konektor dengan tegangan operasi di atas 60V dan terutama bertanggung jawab untuk mengalirkan arus besar.
Konektor tegangan tinggi terutama digunakan pada sirkuit tegangan tinggi dan arus tinggi pada kendaraan listrik. Konektor ini bekerja dengan kabel untuk menyalurkan energi dari baterai melalui berbagai sirkuit listrik ke berbagai komponen dalam sistem kendaraan, seperti baterai, pengontrol motor, dan konverter DCDC. Konektor tegangan tinggi seperti konverter dan pengisi daya juga digunakan.
Saat ini, terdapat tiga sistem standar utama untuk konektor tegangan tinggi, yaitu konektor standar LV, konektor standar USCAR, dan konektor standar Jepang. Di antara ketiga konektor ini, LV saat ini memiliki sirkulasi terbesar di pasar domestik dan standar proses terlengkap.
Diagram proses perakitan konektor tegangan tinggi
Struktur dasar konektor tegangan tinggi
Konektor tegangan tinggi terutama terdiri dari empat struktur dasar, yaitu kontaktor, isolator, cangkang plastik dan aksesori.
(1) Kontak: bagian inti yang melengkapi sambungan listrik, yaitu terminal pria dan wanita, buluh, dll.;
(2) Isolator: mendukung kontak dan memastikan isolasi antara kontak, yaitu cangkang plastik bagian dalam;
(3) Cangkang plastik: Cangkang konektor memastikan keselarasan konektor dan melindungi seluruh konektor, yaitu cangkang plastik luar;
(4) Aksesoris: termasuk aksesoris struktural dan aksesoris instalasi, yaitu pin pemosisian, pin pemandu, cincin penghubung, cincin penyegel, tuas putar, struktur pengunci, dll.
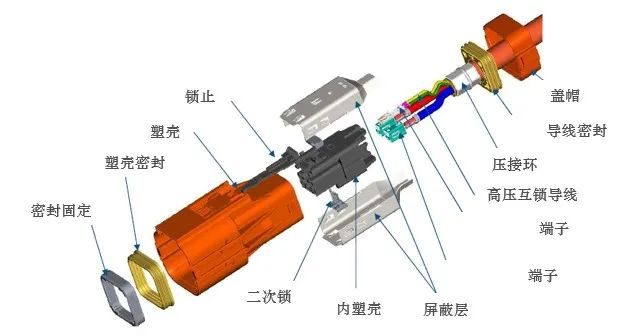
Tampilan meledak konektor tegangan tinggi
Klasifikasi konektor tegangan tinggi
Konektor tegangan tinggi dapat dibedakan dalam beberapa cara. Klasifikasi konektor dapat ditentukan berdasarkan fungsi pelindung, jumlah pin konektor, dan sebagainya.
1.Apakah ada perisai atau tidak
Konektor tegangan tinggi dibagi menjadi konektor tanpa pelindung dan konektor berpelindung berdasarkan adanya fungsi pelindung.
Konektor tanpa pelindung memiliki struktur yang relatif sederhana, tanpa fungsi pelindung, dan biaya yang relatif rendah. Konektor ini digunakan di lokasi yang tidak memerlukan pelindung, seperti peralatan listrik yang dilapisi casing logam seperti sirkuit pengisian daya, bagian dalam kemasan baterai, dan bagian dalam kontrol.
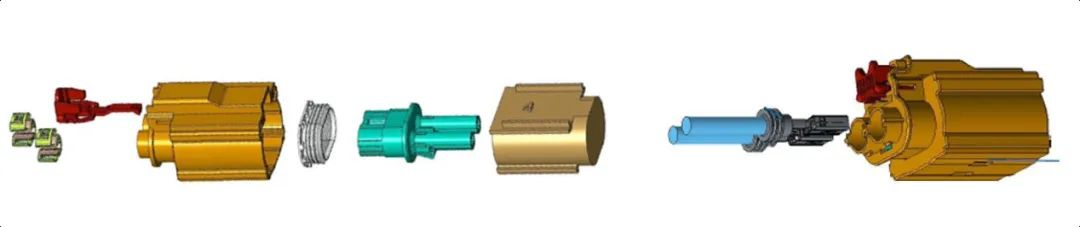
Contoh konektor tanpa lapisan pelindung dan tanpa desain interlock tegangan tinggi
Konektor berpelindung memiliki struktur yang kompleks, persyaratan pelindung, dan biaya yang relatif tinggi. Konektor ini cocok untuk tempat-tempat yang membutuhkan fungsi pelindung, seperti di mana bagian luar peralatan listrik terhubung ke kabel tegangan tinggi.
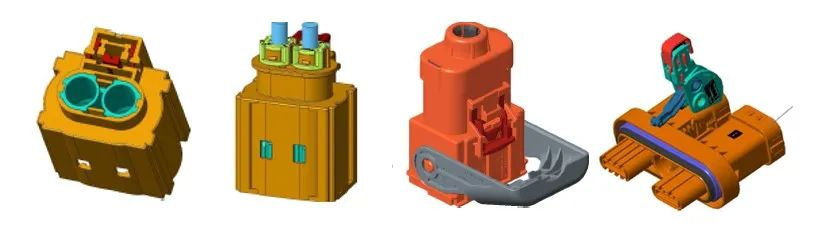
Konektor dengan desain pelindung dan HVIL Contoh
2. Jumlah colokan
Konektor tegangan tinggi dibagi berdasarkan jumlah port koneksi (PIN). Saat ini, konektor yang paling umum digunakan adalah konektor 1P, konektor 2P, dan konektor 3P.
Konektor 1P memiliki struktur yang relatif sederhana dan biaya rendah. Konektor ini memenuhi persyaratan pelindung dan kedap air untuk sistem tegangan tinggi, tetapi proses perakitannya agak rumit dan pengoperasiannya kurang optimal. Umumnya digunakan pada baterai dan motor.
Konektor 2P dan 3P memiliki struktur yang kompleks dan biaya yang relatif tinggi. Konektor ini memenuhi persyaratan pelindung dan kedap air untuk sistem tegangan tinggi dan memiliki kemudahan perawatan yang baik. Umumnya digunakan untuk input dan output DC, seperti pada baterai tegangan tinggi, terminal pengontrol, terminal output DC pengisi daya, dll.
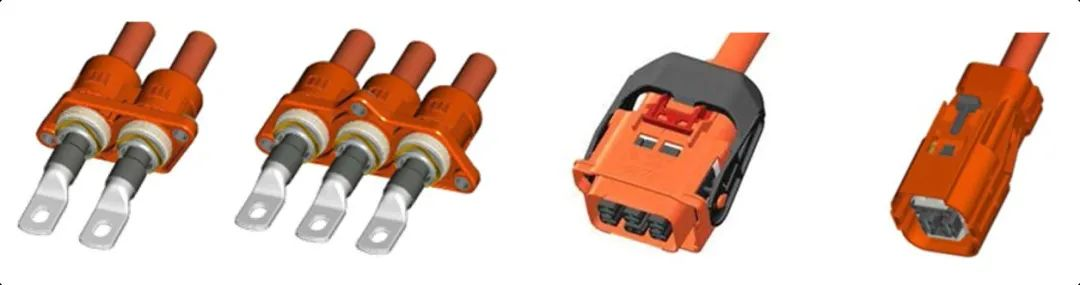
Contoh konektor tegangan tinggi 1P/2P/3P
Persyaratan umum untuk konektor tegangan tinggi
Konektor tegangan tinggi harus mematuhi persyaratan yang ditentukan oleh SAE J1742 dan memiliki persyaratan teknis berikut:
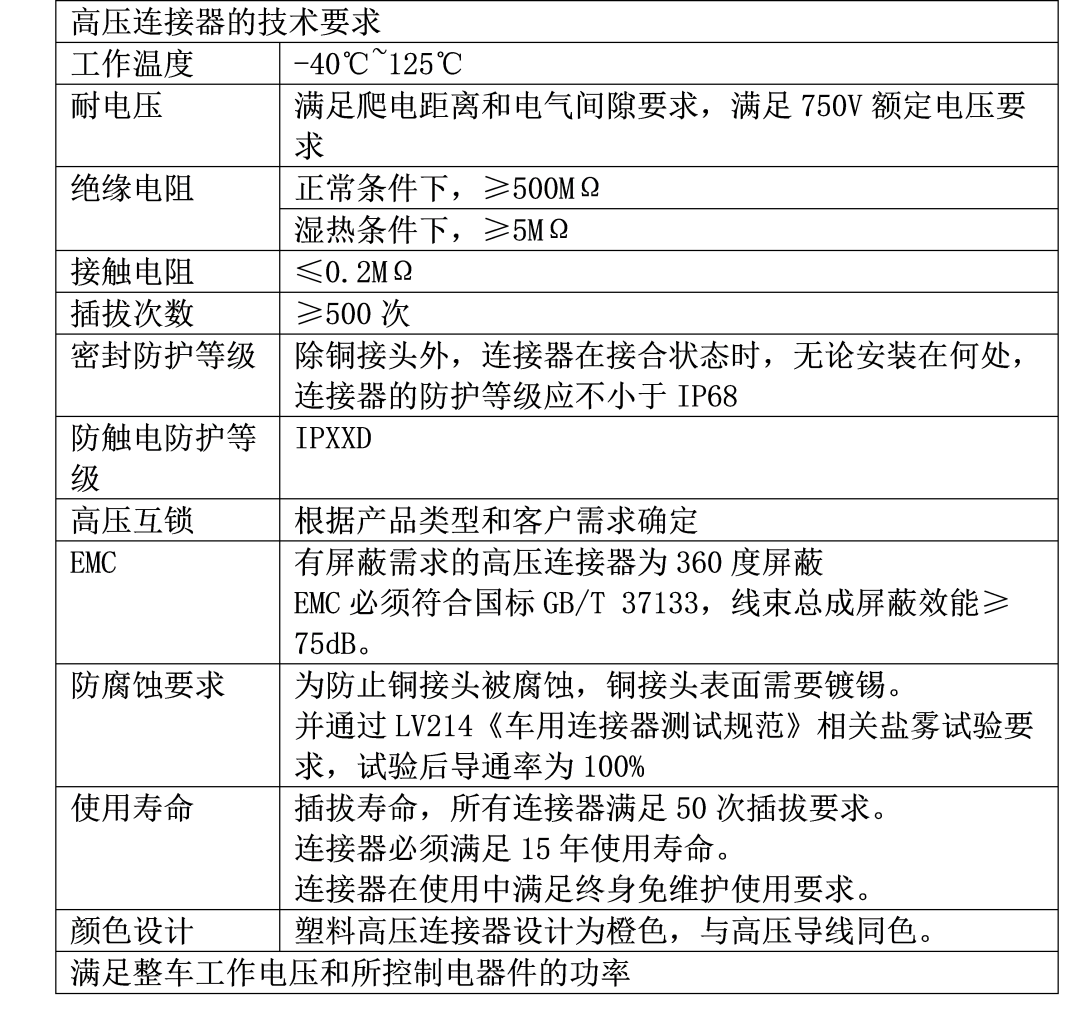
Persyaratan teknis yang ditentukan oleh SAE J1742
Elemen desain konektor tegangan tinggi
Persyaratan untuk konektor tegangan tinggi dalam sistem tegangan tinggi meliputi tetapi tidak terbatas pada: kinerja tegangan tinggi dan arus tinggi; kebutuhan untuk dapat mencapai tingkat perlindungan yang lebih tinggi dalam berbagai kondisi kerja (seperti suhu tinggi, getaran, benturan benturan, tahan debu dan air, dll.); Memiliki kemampuan pemasangan; memiliki kinerja pelindung elektromagnetik yang baik; biaya harus serendah mungkin dan tahan lama.
Berdasarkan karakteristik dan persyaratan di atas yang seharusnya dimiliki konektor tegangan tinggi, pada awal perancangan konektor tegangan tinggi, elemen-elemen desain berikut perlu dipertimbangkan dan dilakukan perancangan yang ditargetkan serta verifikasi pengujian.
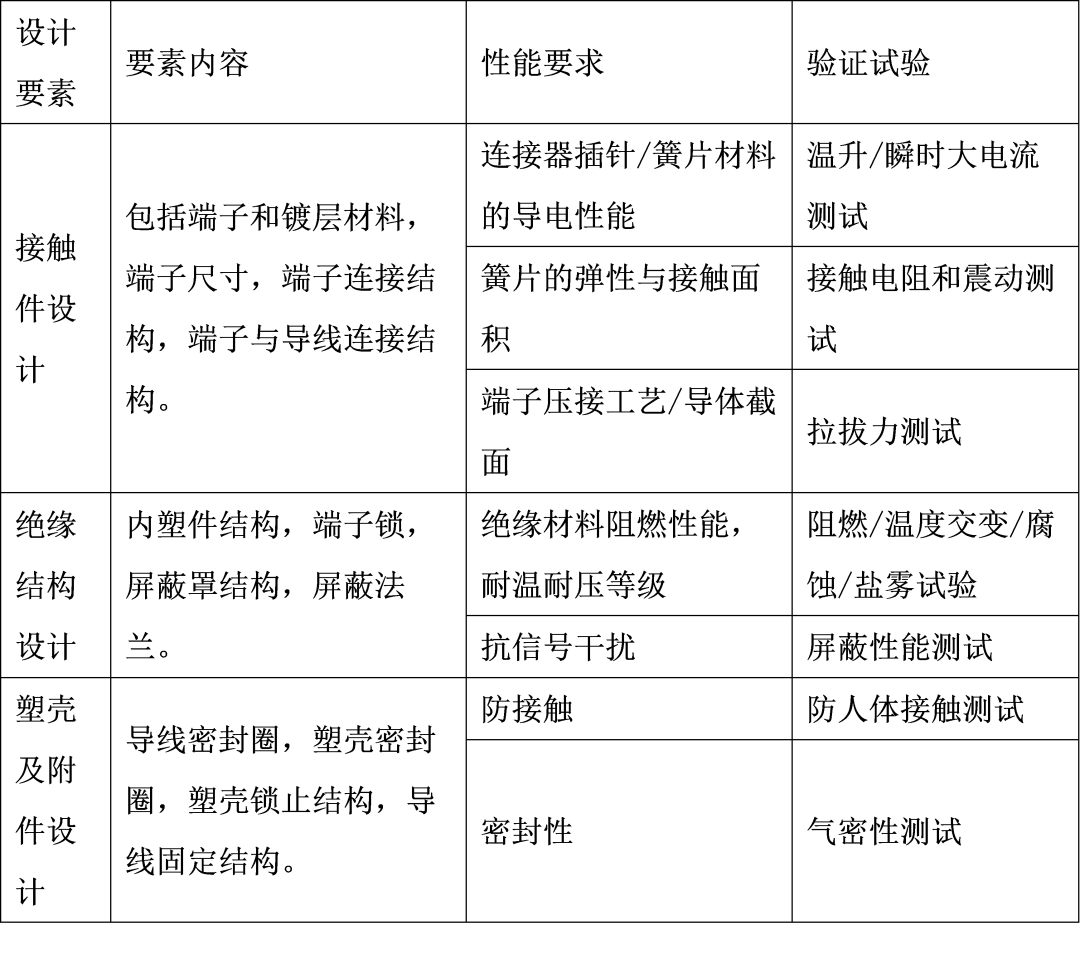
Daftar perbandingan elemen desain, kinerja yang sesuai, dan uji verifikasi konektor tegangan tinggi
Analisis kegagalan dan pengukuran yang sesuai dari konektor tegangan tinggi
Untuk meningkatkan keandalan desain konektor, mode kegagalannya harus dianalisis terlebih dahulu sehingga pekerjaan desain preventif yang sesuai dapat dilakukan.
Konektor biasanya memiliki tiga mode kegagalan utama: kontak buruk, isolasi buruk, dan fiksasi longgar.
(1) Untuk kontak yang buruk, indikator seperti resistansi kontak statis, resistansi kontak dinamis, gaya pemisahan lubang tunggal, titik sambungan dan resistansi getaran komponen dapat digunakan untuk menilai;
(2) Untuk isolasi yang buruk, resistansi isolasi isolator, tingkat degradasi waktu isolator, indikator ukuran isolator, kontak dan bagian lain dapat dideteksi untuk menilai;
(3) Untuk keandalan tipe tetap dan terpisah, toleransi perakitan, momen ketahanan, gaya retensi pin penghubung, gaya penyisipan pin penghubung, gaya retensi dalam kondisi tekanan lingkungan dan indikator lain dari terminal dan konektor dapat diuji untuk menilai.
Setelah menganalisis mode kegagalan utama dan bentuk kegagalan konektor, tindakan berikut dapat diambil untuk meningkatkan keandalan desain konektor:
(1) Pilih konektor yang sesuai.
Pemilihan konektor tidak hanya harus mempertimbangkan jenis dan jumlah sirkuit yang terhubung, tetapi juga harus mempertimbangkan komposisi peralatan. Misalnya, konektor melingkar lebih tahan terhadap iklim dan faktor mekanis dibandingkan konektor persegi panjang, memiliki keausan mekanis yang lebih sedikit, dan terhubung dengan andal ke ujung kabel, sehingga konektor melingkar harus dipilih sesering mungkin.
(2) Semakin banyak jumlah kontak pada suatu konektor, semakin rendah keandalan sistemnya. Oleh karena itu, jika ruang dan berat memungkinkan, cobalah memilih konektor dengan jumlah kontak yang lebih sedikit.
(3) Saat memilih konektor, kondisi kerja peralatan harus dipertimbangkan.
Hal ini karena arus beban total dan arus operasi maksimum konektor sering kali ditentukan berdasarkan panas yang diizinkan saat beroperasi pada kondisi suhu tertinggi di lingkungan sekitar. Untuk mengurangi suhu kerja konektor, kondisi pembuangan panas konektor harus dipertimbangkan secara menyeluruh. Misalnya, kontak yang lebih jauh dari pusat konektor dapat digunakan untuk menghubungkan catu daya, yang lebih kondusif untuk pembuangan panas.
(4) Tahan air dan anti korosi.
Jika konektor bekerja di lingkungan dengan gas dan cairan korosif, untuk mencegah korosi, perhatikan kemungkinan memasangnya secara horizontal dari samping selama pemasangan. Jika kondisi mengharuskan pemasangan vertikal, cairan harus dicegah mengalir ke konektor di sepanjang kabel. Umumnya, gunakan konektor tahan air.
Poin-poin penting dalam desain kontak konektor tegangan tinggi
Teknologi sambungan kontak terutama memeriksa area kontak dan gaya kontak, termasuk sambungan kontak antara terminal dan kabel, dan sambungan kontak antara terminal.
Keandalan kontak merupakan faktor penting dalam menentukan keandalan sistem dan juga merupakan bagian penting dari keseluruhan rakitan kabel tegangan tinggi.Karena lingkungan kerja yang keras pada beberapa terminal, kabel, dan konektor, sambungan antara terminal dan kabel, serta sambungan antara terminal dan terminal, rentan terhadap berbagai kegagalan, seperti korosi, penuaan, dan kendur akibat getaran.
Karena kegagalan rangkaian kabel listrik yang disebabkan oleh kerusakan, kelonggaran, jatuh, dan kegagalan kontak menyumbang lebih dari 50% kegagalan pada seluruh sistem kelistrikan, perhatian penuh harus diberikan pada desain keandalan kontak dalam desain keandalan sistem kelistrikan tegangan tinggi kendaraan.
1. Sambungan kontak antara terminal dan kabel
Sambungan antara terminal dan kabel mengacu pada penyambungan keduanya melalui proses crimping atau pengelasan ultrasonik. Saat ini, proses crimping dan pengelasan ultrasonik umum digunakan pada rangkaian kabel tegangan tinggi, masing-masing dengan kelebihan dan kekurangannya sendiri.
(1) Proses crimping
Prinsip proses crimping adalah menggunakan gaya eksternal untuk menekan kawat konduktor secara fisik ke bagian terminal yang di-crimping. Tinggi, lebar, kondisi penampang, dan gaya tarikan terminal crimping merupakan inti dari kualitas terminal crimping, yang menentukan kualitas crimping.
Namun, perlu diperhatikan bahwa struktur mikro permukaan padat yang diproses secara halus selalu kasar dan tidak rata. Setelah terminal dan kabel dikerutkan, yang terjadi bukanlah kontak seluruh permukaan kontak, melainkan kontak beberapa titik yang tersebar pada permukaan kontak. Permukaan kontak aktual harus lebih kecil daripada permukaan kontak teoritis, yang juga menjadi alasan tingginya resistansi kontak proses pengeritingan.
Crimping mekanis sangat dipengaruhi oleh proses crimping, seperti tekanan, tinggi crimping, dll. Kontrol produksi perlu dilakukan melalui berbagai cara seperti tinggi crimping dan analisis profil/analisis metalografi. Oleh karena itu, konsistensi crimping dari proses crimping rata-rata, keausan pahat besar, dan keandalannya rata-rata.
Proses crimping mekanis sudah matang dan memiliki beragam aplikasi praktis. Proses ini merupakan proses tradisional. Hampir semua pemasok besar memiliki produk wire harness yang menggunakan proses ini.
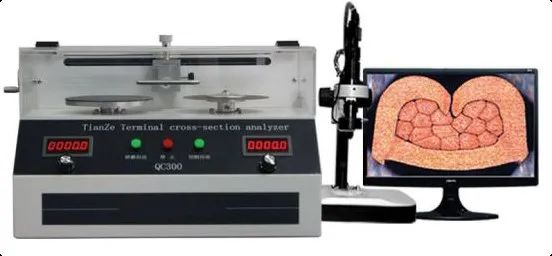
Profil kontak terminal dan kawat menggunakan proses crimping
(2) Proses pengelasan ultrasonik
Pengelasan ultrasonik menggunakan gelombang getaran frekuensi tinggi untuk dipancarkan ke permukaan dua objek yang akan dilas. Di bawah tekanan, permukaan kedua objek saling bergesekan untuk membentuk fusi antar lapisan molekul.
Pengelasan ultrasonik menggunakan generator ultrasonik untuk mengubah arus 50/60 Hz menjadi energi listrik 15, 20, 30, atau 40 kHz. Energi listrik frekuensi tinggi yang telah dikonversi diubah kembali menjadi gerakan mekanis dengan frekuensi yang sama melalui transduser, kemudian gerakan mekanis tersebut ditransmisikan ke kepala las melalui serangkaian perangkat horn yang dapat mengubah amplitudo. Kepala las mentransmisikan energi getaran yang diterima ke sambungan benda kerja yang akan dilas. Di area ini, energi getaran diubah menjadi energi panas melalui gesekan, yang melelehkan logam.
Dalam hal kinerja, proses pengelasan ultrasonik memiliki resistansi kontak kecil dan pemanasan arus lebih rendah untuk waktu yang lama; dalam hal keamanan, dapat diandalkan dan tidak mudah kendor dan jatuh di bawah getaran jangka panjang; dapat digunakan untuk pengelasan antara bahan yang berbeda; dipengaruhi oleh oksidasi permukaan atau pelapisan Selanjutnya; kualitas pengelasan dapat dinilai dengan memantau bentuk gelombang yang relevan dari proses crimping.
Meskipun biaya peralatan proses pengelasan ultrasonik relatif tinggi, dan bagian logam yang akan dilas tidak boleh terlalu tebal (umumnya ≤5mm), pengelasan ultrasonik adalah proses mekanis dan tidak ada arus yang mengalir selama seluruh proses pengelasan, jadi tidak ada Masalah konduksi panas dan resistivitas adalah tren masa depan pengelasan kabel tegangan tinggi.
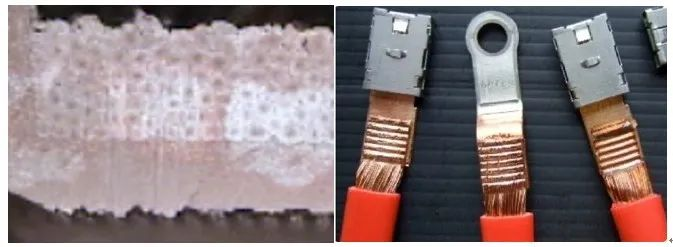
Terminal dan konduktor dengan pengelasan ultrasonik dan penampang kontaknya
Terlepas dari proses crimping atau pengelasan ultrasonik, setelah terminal terhubung ke kabel, gaya tariknya harus memenuhi persyaratan standar. Setelah kabel terhubung ke konektor, gaya tarik tidak boleh kurang dari gaya tarik minimum.
Waktu posting: 06-Des-2023